Ceramic Forming Capabilities
The new manufacturing concepts for innovative products fall back on manifold shape forming methods.
The forming process involves 1st forming stage and an optional machining stage, the 1st forming process aims to produce a near net shape part with sufficient strength for subsequent handling (green machining). the 1st forming process used by XMCERA included dry pressing, isostatic pressing, low pressure injection molding and ceramic injection molding.
Forming Processes
- Dry press
Dry pressing is a medium to high volume forming method for parts ranging from the simple (for example discs or plates) to relatively complex (for example parts with holes or recesses). Components made by dry pressing do not usually have any subsequent green machining and where possible are made to as–sintered tolerances. -
Isostatic Pressing
Isostatic pressing is a small to medium volume forming technique of which there are 2 variations: wet–bag isostatic pressing and dry–bag isostatic pressing. In both cases a spray dried powder is contained in a flexible (usually rubber or polyurethane) bag which is subjected to an isostatic pressure.Wet–bag isostatic pressing(cold isostatic press) is primarily for simple stock shapes such as rods and tube, which are subsequently green machined to the required shape, whereas dry–bag pressing can produce more complex shapes, such as nozzles. -
Low pressure injection molding
In low pressure injection molding (hot molding) flowable suspensions made of a low melting wax-paraffin-ceramic powder mixture are used to produce ceramic components. Due to the low operating temperatures, low injection pressures can be used whereby tool wear is dramatically reduced. It is also possible to use tools made of soft materials like e.g. silicon rubber. -
Ceramic Injection molding
Ceramic injection molding (CIM) offers a near net-shape, large scale production of ceramic components with complex geometry. The basis for the CIM technology forms the so-called feedstock consisting of a homogeneous mixture consisting of the ceramic powder and a thermoplastic binder system. - Green Machining
Green machining is the machining of an un-fired ‘green’ or raw body. This needs to be done when the consolidation method used cannot produce the required shape. For example, the best way to make a part like a weld location pin is to green machine an isostatically pressed rod.
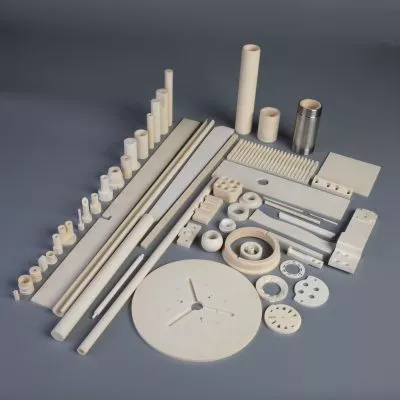
Ceramic Forming Capabilities
We offered services include the creation of manufacturing concepts as well as the rating of production processes under the aspect of costs, quality control und energy efficiency. We support our partners in the development of fine ceramic products from pilot plant to mass production.